



Innovative Stormwater Management at the Parks at Walter Reed: A Model for Urban Development

Effectively managing stormwater runoff can be difficult and challenging for urban planners and developers alike. In Washington, D.C., where the city is susceptible to stormwater runoff and sewer overflow events, managing stormwater runoff is a critical component for protecting public health, the environment, and the city’s infrastructure.
So, it may be no surprise then that in the District of Columbia, where the Dept. of Energy & Environment is the authority for overseeing stormwater management, there are strict construction requirements for on-site stormwater retention, with the overall goal of reducing the burden on the city sewer system to prevent pollution from reaching natural water bodies. The District’s Stormwater Management Regulations stipulate that sites “achieve retention of the rainfall from a 1.2 inch rainfall event, which is the ninetieth (90th) percentile rainfall event for the District of Columbia, measured for a twenty-four (24)-hour rainfall event with a seventy-two (72)-hour antecedent dry period.”
When it came to specifying the new roofs at the former Walter Reed Medical Center site in Northwest Washington, managing stormwater collection and runoff was a high priority.
The Parks at Walter Reed is a 66-acre land development of the historic Walter Reed Army Medical Center site that when fully developed will contain 3.1 million square feet of new construction and adaptive reuse of historic structures, including retail, for-rent and for-sale multifamily units, townhomes, office, healthcare, a school, and a hotel. The development will contain approximately 220,000 square feet of retail, more than 300,000 square feet of office space and ambulatory care, a 200-key hotel and conference center, a top-performing language-immersion school, and 30,000 square feet of creative and arts uses.
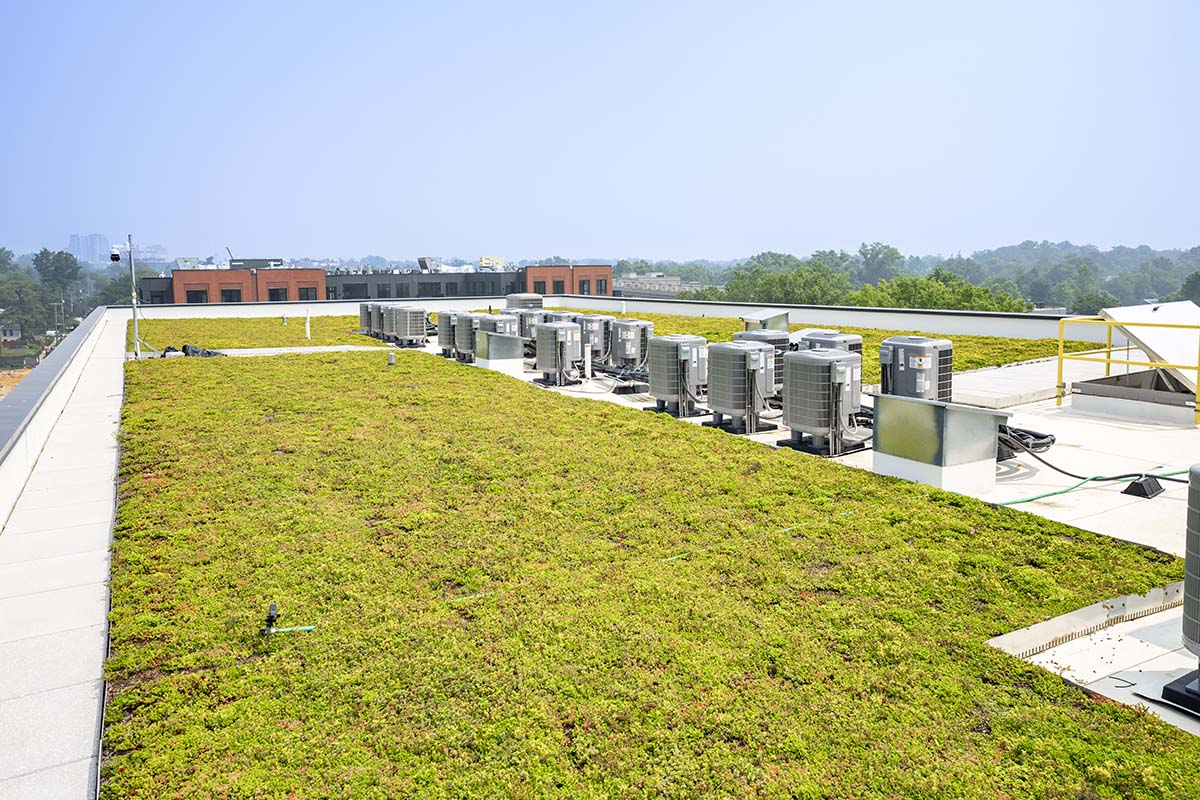
Photo © Carlisle SynTec Systems, click to enlarge.
In addition, the project will include nearly 2,100 units of high-quality housing to serve a diverse mix of incomes and households, providing both rental and homeownership options, as well as new roads and infrastructure and nearly 20 acres of parks and plazas, all employing energy saving and water conserving tools.
Two of the sites’ new buildings -- named The Hartley and Clover at the Parks -- are both six-story mixed use facilities. Both are stick built over concrete podiums, and both have wood roof decks. According to Washington’s strict stormwater management system, each had to be designed to treat and manage stormwater and to meet a specific green area ratio on site.
The facilities were designed and specified by the Washington office of the global architectural firm Torti Gallas + Partners, and managed by Julian Goldman, Associate Principal and Scott Welch, Senior Principal.
“This is a significant redevelopment project, involving mixed use residential and retail facilities,” said Goldman. “The Hartley has a Whole Foods store, fitness center, and pet grooming at the street level plus 323 apartments, from studios to three-bedroom units, above. The building features two interior courtyards – one with a pool and amenity space, and the other with a Zen garden. Clover at the Parks is a 60-unit co-living community comprised of 248 individually rentable bedrooms in two- to five-unit configurations. The facility also includes 24,000 square feet of street-level retail space, a lounge, library, fitness center, conference room, game room, elevated courtyard areas, as well as a sixth-floor observation deck.”
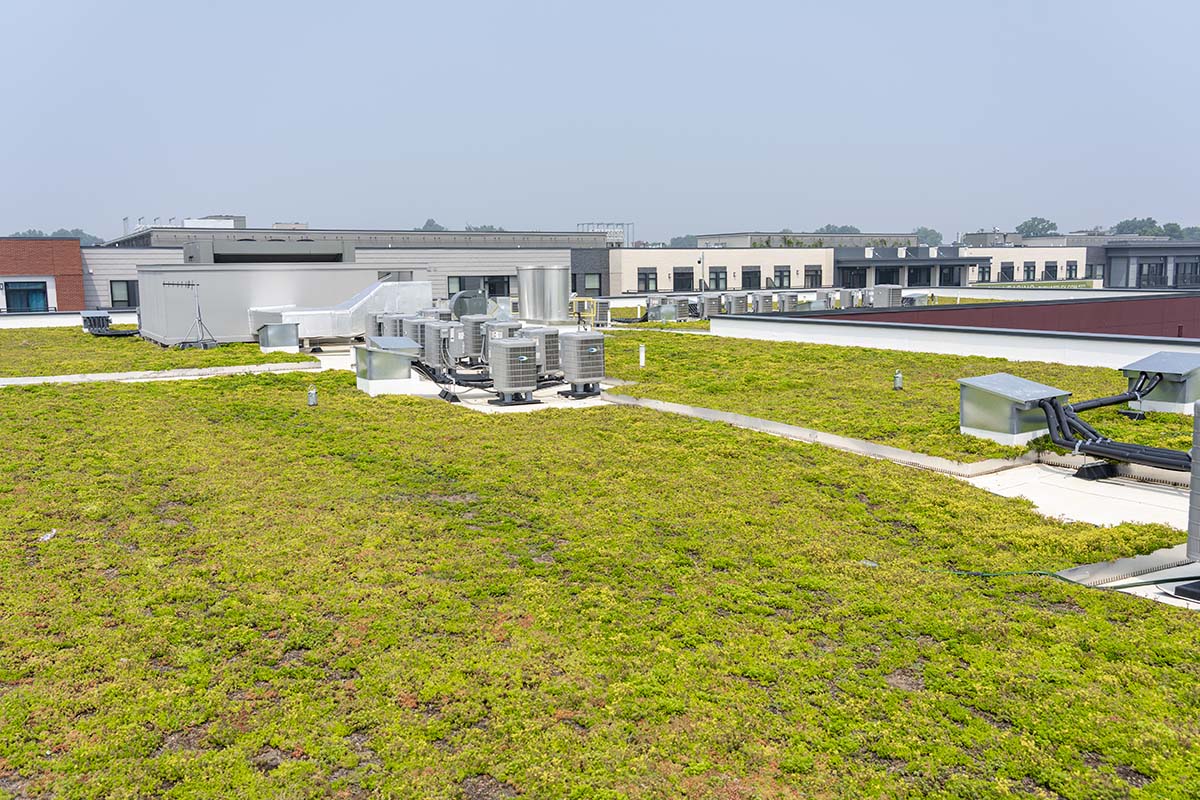
Photo © Carlisle SynTec Systems
The LEED® Gold facilities were built by CBG Building Company. Elite Sheet Metal Works, marketed under the name, Roofing by Elite, of Beltsville, Maryland, an NRCA Contractor and multiple year winner of Carlisle’s prestigious Perfection Award for exceptional installation quality, was hired to install the green roofs on the two mixed use facilities. In total, the two facilities include 84,200 square feet of roofing, and approximately 51,400 square feet of vegetative green roofing, which accounted for approximately 61% of the total roof area.
“We specialize in installing green roofs,” said Joe Gretchen, an owner and principal with Roofing by Elite (Elite). “We’ve installed many green roofs over the years, and the Parks was an exceptional project for us.”
Since this was new construction, the roofing work had to be completed in sections as construction allowed. In addition, it was a very congested and tight construction area, so Elite had to load the roof several times as its crew of eight to twelve worked across the facility as the roof was installed.
Roof installation began amid the COVID-19 pandemic and its associated supply chain challenges. Securing the materials needed for the project was challenging, but in partnership with Carlisle, Elite was able to complete installation in a timely fashion.
“At the time, the supply chain was an issue everywhere, so securing the roofing materials needed for the project turned out to be a major challenge, which we eventually got through,” said Gretchen.
The Roofing Assembly
From the plywood deck up, the roofing assembly consists of Carlisle’s self-adhered VapAir Seal™ 725TR Air & Vapor Barrier/Temporary Roof, a 40-mil membrane composed of 35-mils of self-adhering rubberized asphalt laminated to a 5-mil woven polypropylene film.
“The vapor barrier also acts as a temporary roof,” said Gretchen, “so once that was fully down, the facility was essentially dried-in.”
With the vapor barrier down, the Elite crew loose-laid two layers of 2.6-inch Carlisle polyisocyanurate insulation, with staggered joints to reduce thermal bridging. The insulation was topped and protected by a layer of 4 x 8-ft. sheets of ½-inch SECUROCK® Gypsum-Fiber Roof Board to provide a flat and firm substrate for the roof garden assembly.
Once the insulation and cover board were in place, Elite installed Carlisle’s 80-mil white Sure-Weld EXTRA TPO membrane. Sure-Weld TPO membranes are made with advanced polymerization technology that combines the flexibility of ethylene-propylene (EP) rubber with the heat weldability of polypropylene. Additionally, Sure-Weld TPO membranes feature OctaGuard XT™, an industry-leading, state-of-the-art weathering package for long term performance.
Elite fully adhered the membrane with Carlisle’s CAV-GRIP III Adhesive/Primer, a single-component, low-VOC (less than 250 g/L), spray-applied aerosol contact adhesive and primer.
“We like the simplicity of the CAV-GRIP product. We use the larger, refillable canisters, and it’s quick to apply and flash-off,” said Gretchen, “so we can be very productive with it.”
Once the membrane was down, Elite stripped in the seams where the overburden was to be installed with cover strip.
“It’s a bit of extra time and labor, but for us it’s standard practice on all green roofs, and Carlisle also requires it as added protection,” said Gretchen.
Both rooftops include 30-inch-tall parapet walls around the perimeter. To terminate the membrane, the crew from Elite mechanically fastened the TPO at the base of the parapet, then welded another section of membrane at the base which was secured up and over the top using the CAV-GRIP III Adhesive. A shop-fabricated coping cap made from Carlisle’s flat metal sheets was installed on top of the parapet wall to finish the termination. A three-foot wide walkway around the perimeter and to the mechanicals allows for periodic roof inspections, as well as maintenance access to the mechanical equipment on the roof.

Photo © Carlisle SynTec Systems
Carlisle Roof Garden Sections
The first step for installing the roof garden was to map out the specific areas on each roof section that would eventually house the growth media. For this, the Elite crew snapped lines and installed Carlisle’s Roof Garden Aluminum Edge, which they secured directly to the TPO membrane using Carlisle’s membrane primer and three-inch-wide SecurTAPE™.
“Laying out each area and installing the aluminum edge was somewhat time consuming, because we had to be very precise with the measurements,” said Gretchen. “Plus, we had to build a separate area at the base of the penthouse for a deeper layer of growth media for a green screen.”
On the Hartley, there’s a penthouse mechanical screen enclosure that stands about 7 feet tall in the center of the roof. To increase the green area ratio on the roof, the architect designed a ‘green screen’ in front of the structure which would eventually hold climbing vines to hide the structure. In addition, there were some mechanical and vent units in each green area on 1-foot-tall curbs that had to be carefully flashed before they could install the growth media.
Once the green areas were mapped out and the aluminum edging was in place, Elite loose-laid Carlisle’s 200V Protection Fabric in each area. The non-woven polyproplylene fabric, which is designed to resist soil, chemicals, mildew, acids, and alkalis, provides protection to the TPO membrane below and serves as a drainage filter.
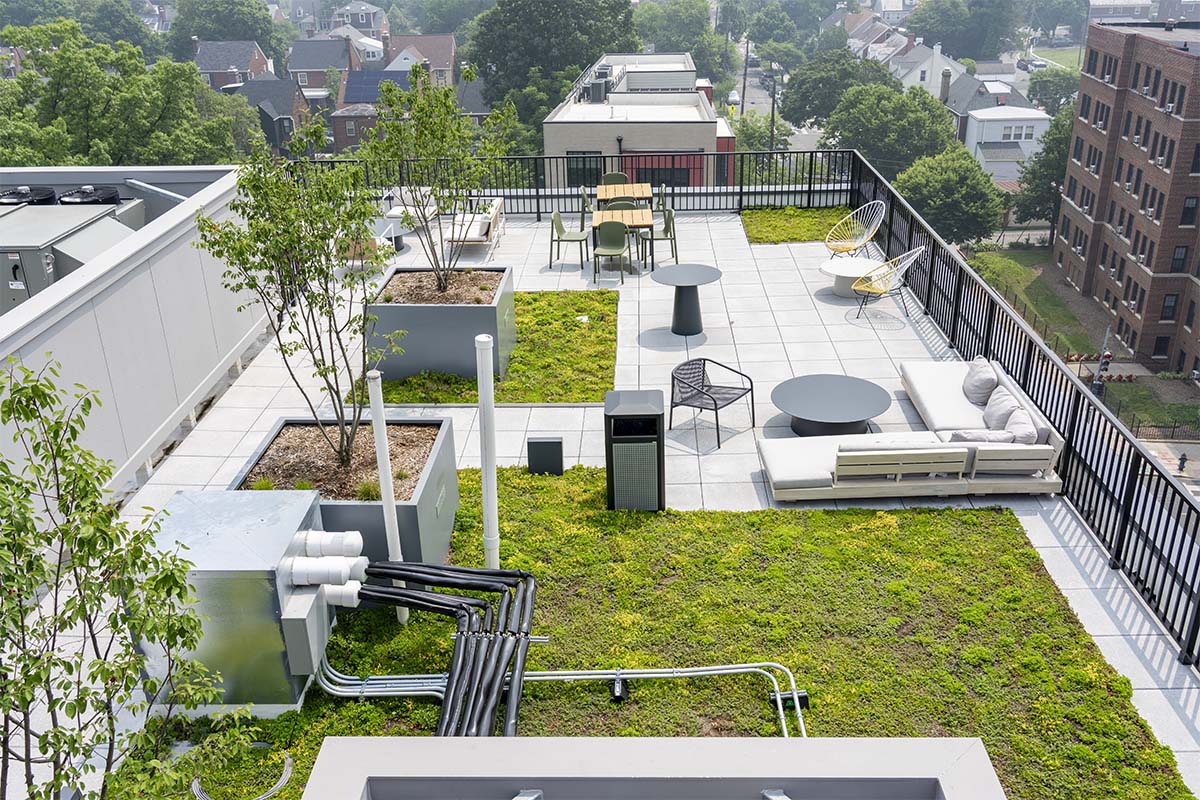
Photo © Carlisle SynTec Systems
The next step was loose-laying Carlisle MiraDRAIN® 9800, a non-woven filter fabric bonded to a molded polypropylene core, that offers superior filtration and prevents small particles from clogging drainage channels in the aluminum edging.
For projects requiring stringent stormwater management, a mineral wool blanket is integrated into the assembly to optimize water retention. For this project, Elite installed Carlisle’s Roof Garden Hydro-blanket D13, a 1-inch-thick mineral wool blanket that provides superior water retention and filtration and helps promote root growth and healthy vegetation.
“We installed two layers of 1-inch-thick mineral wool insulation on top of the MiraDRAIN,” said Gretchen. “Mineral wool is great for reducing stormwater runoff and ideal for green roof applications like this one.”
Four inches of Carlisle Growth Media was then installed over the top. For that the crew from Elite used an outside service to have the growth media blown onto the roof and into each garden area. Then the crew carefully raked the media to the correct depth and compacted the media with a 250-lb. roller.
The last step was to install Carlisle Vegetated Sedum Mats, which are pre-grown with 17 different varieties of sedums for applications in most climate zones.
“The mats are about 3-feet-wide by 6.5-feet-long,” said Gretchen. “We first wet down the growth media and then rolled out the mats to fit within the garden areas. The nice thing with the mats is you get instant vegetative coverage, so the roof looks great from the start.”
To keep the roof garden green and growing, the Hartley has a 90,000-gallon cistern in the basement collecting water runoff from the building. That water is pumped back to the roof to a pop-up sprinkler system installed in the garden areas for watering. This irrigation system can be activated for sedum maintenance as needed, but also automatically runs after a rain event to contribute to required stormwater treatment capacity for the site.
“Overall, the project went very well. We had a great crew on the project, and we worked really well with the general contractor, and with Carlisle to get all of the roofing and green roof materials to the project on time,” said Gretchen.
At the end of the day, the roof gardens at the Parks at Walter Reed benefit the local community in several ways. Not only do they help alleviate stormwater runoff, but the green roof can help extend the life of the roofing membrane by protecting it from extreme temperature fluctuations, as well as from ultraviolet radiation. In addition, the green roofs can help reduce the local urban heat island effect, since they minimize emissivity, and can help lower nearby air temperatures. Lastly, green roofs like the ones on the Hartley and the Clover at the Parks buildings are visually pleasing for the residents.
Project Information
Project Location: Washington, DC
Carlisle Applicator: Elite Sheet Metal Works
Building Owner: Hines Properties
Architect: Torti Gallas + Partners
Roofing System: Carlisle Sure-Weld® TPO, adhered with CAV-GRIP® III in a roof garden application
Carlisle SynTec Systems, a segment of Carlisle Construction Materials, LLC, has produced single-ply membrane roofing systems for over 50 years. Headquartered in Carlisle, Pa., with facilities in Pa., Ill., Miss., and Utah. Call 800-479-6832 or visit www.carlislesyntec.com for more information.